Friday, 22 November 2024
DIY Small Pallet Shed: A Practical Project for Budget-Conscious Builders

DIY Small Pallet Shed: A Practical Project for Budget-Conscious Builders
Dreaming of extra storage space without breaking the bank? A DIY pallet shed offers a fantastic solution! This project combines rustic charm with practical functionality, utilizing repurposed materials to minimize costs and maximize your creative potential. Forget expensive pre-fabricated structures; with a little planning and elbow grease, you can build a charming and surprisingly sturdy shed using reclaimed pallets. This guide will walk you through each step, empowering you to create a personalized storage solution perfect for your backyard or garden.
Planning Your Pallet Shed
Before diving into construction, meticulous planning ensures a smooth and successful project. First, determine the desired dimensions of your shed. Consider the space available and the amount of storage you need. A small shed, even just 4ft x 4ft, can hold a surprising amount of gardening tools, outdoor equipment, or seasonal decorations. Next, source your pallets. Inspect them carefully for any signs of rot, damage, or pest infestations. Clean the pallets thoroughly, removing any loose nails or debris. Remember to check local building codes and regulations concerning shed construction and ensure your chosen location on your property is compliant.
Essential Tools and Materials
Gather your tools and materials beforehand to streamline the building process. Youâll need:
- Reclaimed pallets (the number will depend on the size of your shed)
- Hammer
- Screws (exterior-grade)
- Drill/Driver
- Measuring tape
- Level
- Saw (circular saw or hand saw)
- Safety Glasses
- Work gloves
- Optional: Roofing materials (e.g., corrugated metal, shingles)
- Optional: Wood preservative or paint
Constructing the Shed Frame
Start by creating the base frame of your shed. This provides a strong foundation for the walls and roof. You can use additional lumber for added stability, especially if your pallets are less sturdy. Lay out the pallets according to your plan, ensuring theyâre level and aligned. Secure the pallets together using screws, paying close attention to creating strong, square corners. Remember safety first â" always wear safety glasses when using power tools.
Building the Walls and Roof
Once the base is complete, construct the walls using the remaining pallets. You can choose to build solid walls or leave some gaps for ventilation. For extra stability, consider using additional support beams inside the structure. The roof construction will depend on your design preference. A simple gable roof is relatively easy to build using more pallets or lumber, ensuring you create a sufficient overhang to protect the walls from the elements. Secure the roof firmly to the walls with screws.
Finishing Touches and Customization
After completing the main structure, add the finishing touches to personalize your pallet shed. Consider adding a door using reclaimed wood or even a repurposed door from a previous project. You can enhance the aesthetic appeal and weather resistance with a coat of exterior-grade paint or wood preservative. For additional protection from the elements, consider adding roofing felt or shingles to the roof. Add hinges and a handle to your door and finally, step back and admire your newly built, budget-friendly pallet shed!
Ideas for Personalization
Let your creativity shine! Add windows for natural light, a small shelf for storage, or even a decorative trellis for climbing plants. The possibilities are endless! A little bit of personal flair can transform this practical project into a charming and unique addition to your outdoor space. Remember to take pictures along the way to document your hard work and share your accomplishment!
How to Create a Functional Small Pallet Shed for Your Yard

Building Your Dream (Mini) Pallet Shed: A Totally Doable DIY Project
So, you've got a bunch of stuff piling up in the garage, the garden shed's bursting at the seams, and you're dreaming of a little extra storage space? Let's face it, sometimes a full-blown shed feels like a bit much, right? That's where a charming, functional, and surprisingly easy-to-build pallet shed comes in! This isn't some flimsy thing that'll fall apart after a good sneeze â" we're talking about a sturdy, weather-resistant addition to your yard that'll actually *work*. And the best part? It's way more achievable (and affordable!) than you might think.
Planning Your Pallet Paradise: Size, Location, and Design
Before you even think about grabbing a hammer, let's get the planning sorted. This isn't rocket science, but a little forethought will save you a lot of headaches down the line.
Sizing Up Your Needs:
Think realistically about what you'll be storing. Are we talking garden tools, outdoor cushions, or maybe even some extra firewood? A small shed, even just 4ft x 4ft, can hold a surprising amount! Remember to factor in the space you'll need to actually *access* those things. You don't want to build a tiny shed and then find you can't get to anything inside.
Location, Location, Location:
Consider sunlight, access, and drainage. You want a spot that's relatively level and well-drained, away from overhanging trees (to avoid leaf litter and potential damage) and ideally close enough to your house for easy access, but not so close that it looks out of place.
Sketching Out Your Shed:
Even a quick sketch on a napkin can help clarify the overall design. Will it have a door? Windows? A simple lean-to style is great for beginners, while a more enclosed structure will offer better protection from the elements. Decide on the basic shape and dimensions before you start collecting pallets.
Sourcing Your Palettes: The Free (or Cheap!) Foundation
The beauty of a pallet shed is the potential to source materials for next to nothing! Check with local businesses: bakeries, breweries, and construction sites often have pallets they're happy to get rid of. Just be sure to check their condition. You'll need pallets that are sturdy and free from rot or significant damage. Remember to ask permission before taking any pallets, even if they look abandoned. And please always be mindful of the environment and only take pallets you're confident are being disposed of.
If you can't find free pallets, you can often buy them relatively cheaply from reclamation yards or online marketplaces. This adds cost, but might be necessary if you can't locate enough suitable free ones.
Building Your Pallet Powerhouse: A Step-by-Step Guide
Once you have your pallets, let's build! This is a simplified guide, and the exact method will depend on your design. But the basic principles remain the same.
Preparation is Key:
Constructing the Base:
You'll need a level base. Consider using concrete slabs, paving stones, or even a layer of compacted gravel. This will prevent rot and make the shed more stable. Assemble your pallets to form the base, securing them with screws and bracing where necessary.
Building the Walls and Roof:
The wall construction will depend on your design. For a simple lean-to, you might simply lean pallets against a wall or fence. For a more enclosed shed, you'll need to build a frame and attach the pallets to it. The roof could be a simple gabled roof made from more pallets, or you could use corrugated roofing sheets for extra durability and weather protection. Secure everything with screws and bracing, paying close attention to strength and stability.
Adding the Finishing Touches:
Once the structure is complete, you can add a door (purchased or creatively fashioned from pallets!), windows (again, repurposed or new), and any other features you desire. Consider adding a latch or lock for security. A lick of paint can transform your pallet shed from rustic to chic â" let your creativity run wild!
Tips for Success (and Avoiding Disasters!):
Frequently Asked Questions
Q: How long does it take to build a pallet shed?
A: This depends on the size and complexity of your design. A simple lean-to could take a weekend, while a more complex shed might take several days or even a week, especially for beginners.
Q: How much does it cost to build a pallet shed?
A: If you can source free pallets, the cost is primarily for tools, screws, sealant, and potentially a door and roofing materials. You might spend anywhere from $50 to $200, depending on your choices.
Q: Are pallet sheds sturdy?
A: Yes, if built correctly using sound pallets and proper construction techniques. The key is careful planning, strong construction, and weatherproofing.
Q: How do I make my pallet shed weatherproof?
A: Thoroughly clean and treat the wood with a quality wood preservative and weatherproof sealant. A solid roof is essential, and consider adding a waterproof membrane or flashing around the edges.
Q: Can I use any type of pallet?
A: No. Only use pallets that are in good condition, free from rot and major damage. Avoid pallets that have been treated with chemicals that are harmful. Heat-treated pallets are generally safe for DIY projects.
Building a pallet shed is a fantastic way to add valuable storage space to your yard without breaking the bank. With a little planning and effort, you can create a functional and attractive structure you'll be proud of for years to come!
Thursday, 21 November 2024
DIY 10x12 Pallet Shed: Step-by-Step Guide for Beginners

DIY 10x12 Pallet Shed: A Beginner's Step-by-Step Guide
Building your own shed can feel daunting, but with careful planning and a methodical approach, even beginners can construct a sturdy and attractive 10x12 pallet shed. This guide provides a detailed, step-by-step process, making your DIY project achievable and rewarding. We'll leverage the readily available and cost-effective material: reclaimed pallets. Prepare to transform discarded wood into a functional and stylish addition to your property!
Planning and Preparation: Laying the Foundation for Success
Before you even touch a pallet, meticulous planning is crucial. This phase ensures a smooth building process and a structurally sound shed. First, obtain the necessary permits from your local council. This step, though seemingly bureaucratic, prevents future headaches. Next, choose a suitable location thatâs level, accessible, and complies with local regulations regarding setbacks from property lines. Consider drainage â" you don't want water pooling around your new shed. Mark out the 10x12 foot area with stakes and string. Finally, gather your materials, including approximately 30-40 reclaimed pallets (inspect them carefully for rot or damage), concrete for the base (if you aren't using existing paving), screws, nails, a level, measuring tape, safety glasses, work gloves, and a saw (circular saw is recommended).
Building the Foundation: A Stable Base for Your Shed
Preparing the Ground
Begin by excavating the marked area to a depth of about 4 inches. Compact the ground thoroughly to provide a stable base. For a truly robust foundation, pour a concrete slab. Alternatively, level the ground and use pre-existing paving stones as a base. Remember to ensure proper drainage away from the shed's foundation to prevent moisture damage.
Constructing the Base Frame
Once the base is set, build the base frame of your shed using pressure-treated lumber for durability. Cut four pieces of lumber to 10 feet and four pieces to 12 feet. Assemble these pieces into a rectangle, creating a sturdy frame. Secure the corners using strong screws or galvanized nails, ensuring the frame is perfectly square and level using a carpenter's square and level.
Erecting the Walls: Bringing Your Shed to Life
This stage involves the creative and somewhat challenging task of assembling the pallet walls. Inspect each pallet thoroughly before use. Discard any that are damaged beyond repair. Start with one wall, arranging the pallets to form a vertical structure. Leave gaps for ventilation as needed. Secure the pallets together using screws or long nails, ensuring they are tightly aligned and level. Repeat this process for all four walls. Remember to account for the door opening when assembling the front wall. This can be achieved by carefully cutting or removing sections of pallets to create the desired doorway.
Installing the Roof: Protecting Your Investment
Construct a simple gable roof using more pressure-treated lumber for the rafters. Attach the rafters to the top of the walls, ensuring they are evenly spaced and securely fastened. Cut plywood sheets to fit the roof and nail them firmly to the rafters. Finally, consider using roofing felt or asphalt shingles to ensure waterproof protection. This final touch protects your shed from rain and other weather elements.
Adding the Finishing Touches: Enhancing Functionality and Aesthetics
Once the roof is complete, consider adding a door (either repurposed from another source or made from more pallets). Install hinges and a latch. You might also want to add windows for extra light and ventilation. To protect the wood, apply a weather-resistant sealant or paint. This will extend the life of your shed and enhance its appearance. Consider adding shelving or other internal features to customize the space to your needs.
Safety First!
Always prioritize safety. Wear appropriate safety gear, including safety glasses and work gloves, throughout the project. Be cautious when using power tools, and take breaks when needed. Never rush the process â" accuracy and careful execution are key to a successful and safe build.
Building a 10x12 pallet shed is a rewarding project that combines creativity, practicality, and cost-effectiveness. By following these steps, you'll create a durable and functional addition to your property. Remember to enjoy the process and take pride in your accomplishment!
How to Build a Pallet Shed for Your Backyard Using Free Plans

Building Your Dream Backyard Pallet Shed: A Step-by-Step Guide Using Free Plans
Hey there, fellow DIY enthusiasts! So you're looking to build a pallet shed, huh? Awesome! Building with reclaimed pallets is a fantastic way to save money and be eco-friendly. Plus, you get that rustic, charming look that everyone loves. This guide will walk you through building your own backyard pallet shed using free plans â" I'll make it as easy as possible, promise!Finding Your Free Pallet Shed Plans
Before we dive into the construction, let's talk about the blueprints. The internet is a treasure trove of free pallet shed plans! A quick Google search for "free pallet shed plans" will unearth a ton of options, ranging from simple lean-tos to more complex structures.Choosing the Right Plan for You
Now, choosing the right plan depends on a few things:- Your skill level: Are you a seasoned DIYer, or are you just starting out? Choose a plan that matches your experience. Simple plans are perfect for beginners.
- The size you need: How much storage space do you require? Consider the dimensions of the pallets you'll be using. Standard pallets are usually 48" x 40", so bear that in mind when selecting your plan.
- The desired features: Do you want a door, windows, a roof overhang? These features will add complexity but can greatly enhance the functionality and aesthetics of your shed.
- The materials you have on hand: Some plans might require specific types of wood or hardware. Check what you already have and choose a plan that minimizes the need for extra purchases.
Gathering Your Materials
Letâs talk about the fun part: gathering your materials! This is where your pallet scavenging skills will come into play.Sourcing Your Pallets
Finding free pallets can be easier than you think! Check with local businesses like grocery stores, construction sites, and even breweries. Many businesses are happy to give away their used pallets. Just make sure to ask for permission before taking any. Remember to inspect the pallets carefully; youâll want to avoid those that are heavily damaged, rotted, or treated with harmful chemicals.
Other Materials Youâll Need
Beyond the pallets themselves, youâll need some additional materials. Your chosen plan will specify the exact quantities, but generally, youâll need:
- Screws: Exterior-grade screws are essential for durability. Choose screws long enough to securely fasten the pallets together.
- Nails (optional): Depending on your plan, you might need nails for certain parts of the construction.
- Wood glue (optional): Adding wood glue can significantly enhance the strength of the joints.
- Roofing material: This could be anything from tar paper to corrugated metal or even recycled shingles. Your plan will guide you on the best option.
- Optional extras: Consider adding things like hinges, a latch for the door, window frames, and paint to personalize your shed.
Building Your Pallet Shed: A Step-by-Step Guide
Now for the exciting part â" building your shed! This is where your free plans will be invaluable. Remember, every plan is different, so follow the instructions carefully. However, here are some general steps you can expect:Preparing the Pallets
Before you start assembling your shed, you'll need to prepare your pallets. This usually involves cleaning them thoroughly, removing any loose nails or splinters, and possibly sanding down any rough edges for safety and a smoother finish. For extra durability and weather protection, consider applying a wood preservative or sealant.
Framing and Assembly
This step involves assembling the base and walls of your shed according to your plan. This might involve stacking and securing pallets together using screws and possibly wood glue. Pay close attention to the planâs specifications on how to connect the pallets to create a structurally sound frame.
Roof Construction
Once the walls are up, it's time to build the roof! This is often the most complex part, depending on the roof design. Your plan will guide you through the process of building the roof frame and attaching your chosen roofing material. Remember to make sure the roof is adequately sloped to allow for proper water drainage.
Adding Doors and Windows (If applicable)
This is where you can add your personal touch! If your plan includes doors and windows, this is the time to install them. Ensure that the hinges and latches are securely fastened for long-term functionality.
Finishing Touches
Once your shed is assembled, it's time for the finishing touches! This could include adding a layer of paint or stain to protect the wood from the elements and give your shed a more polished look. You can also add any extra features you'd like, such as shelves for extra storage.
Safety First!
Remember safety first throughout the entire process. Always wear appropriate safety gear, such as safety glasses and work gloves. Use caution when handling tools and materials, and ask for help if needed. If you are unsure about any aspect of the construction, don't hesitate to seek advice from an experienced DIYer or builder.
Commonly Asked Questions
Q: How long does it take to build a pallet shed?
A: The construction time varies greatly depending on the shed's size and complexity, your experience level, and the availability of your materials. Expect to spend anywhere from a weekend to several weekends to complete the project.
Q: What kind of permits do I need?
A: This depends on your local building codes and regulations. Some jurisdictions require permits for structures of a certain size or complexity. It is wise to check with your local council before starting construction.
Q: Can I use treated pallets?
A: Generally, you shouldnât use treated pallets intended for industrial purposes, as they may contain harmful chemicals. If you decide to use treated pallets, ensure they are designed for outdoor use and comply with all relevant safety regulations.
Q: How can I make my pallet shed more weather resistant?
A: Applying a weather-resistant sealant or paint is a must. Properly sealing the gaps between pallets will also help keep the elements out.
And there you have it! Building a pallet shed is a rewarding project that can add a great deal of value to your backyard. Remember to take your time, follow your chosen plans, and most importantly, have fun! Happy building!Simple Basic Shed Plans for DIYers Who Want to Start Small

Simple Shed Plans for Beginner DIYers
Building your own shed is a rewarding project, offering a sense of accomplishment and a valuable addition to your property. But the prospect of tackling a large-scale construction project can feel daunting, especially for beginners. This guide focuses on crafting a simple, small shed perfect for first-time builders. We'll walk you through the process, ensuring you'll feel confident and empowered throughout the construction. Forget complicated blueprints and overwhelming instructions; this plan emphasizes straightforward design and easy-to-source materials. Let's get started on your DIY shed adventure!
Planning Your Mini-Shed
Before grabbing your tools, meticulously plan your shed's dimensions and features. Consider the purpose of your shed â" will it house gardening tools, bicycles, or other equipment? This dictates the necessary size. A smaller shed, measuring approximately 6ft x 4ft (1.8m x 1.2m) is an excellent starting point for a first-time builder. This compact size simplifies the project significantly while still providing ample storage. Remember to check local building codes to ensure your shed complies with regulations. Don't rush this step; proper planning prevents costly mistakes and ensures a smoother build.
Choosing Your Materials
Opt for readily available and easy-to-handle materials. Pressure-treated lumber is ideal for the frame, offering durability and resistance to rot and insects. For the siding, consider using inexpensive, readily available materials like plywood or composite panels. This will save both time and money. Remember to purchase screws, nails, and any other necessary hardware. Creating a detailed materials list before you begin shopping will prevent unexpected trips back to the hardware store. Accuracy is key here â" buy slightly more than your calculations suggest to account for any potential errors or cuts.
Constructing the Shed Frame
The foundation forms the base of your entire project. A simple concrete slab is perfect for a small shed. Alternatively, a well-prepared and level ground with landscaping fabric and gravel will work well. Start constructing the floor frame using the pressure-treated lumber. Create a sturdy rectangular frame, ensuring all corners are square and the frame is perfectly level. Next, build the walls, attaching them to the floor frame with screws. Make sure to reinforce the corners with extra bracing for stability. Precision is crucial in this stage to ensure a plumb and stable structure.
Adding the Roof and Siding
A simple gable roof is easy to construct for beginners. Construct the roof frame using pressure-treated lumber, ensuring appropriate slope for water runoff. Secure the roofing materialâ"consider asphalt shingles for ease of installationâ"to the roof frame using appropriate fasteners. Finally, attach the chosen siding to the walls, ensuring even spacing and alignment. Remember to leave appropriate gaps for ventilation. Take your time and check your work frequently to maintain structural integrity.
Finishing Touches and Considerations
Once the main structure is complete, add the finishing touches. This includes a simple door and any desired windows for light and ventilation. Consider adding a layer of paint or sealant for protection against the elements. While a lock isn't strictly necessary for a small shed, it provides an added security feature. For a more polished look, trim the edges and fill any gaps in the siding. Adding these details will elevate the final appearance of your shed. Remember to check your local building codes for any requirements regarding permits or inspections.
Essential Tools
Gather these essential tools before you begin:
- Measuring tape
- Level
- Drill/Driver
- Circular saw
- Hammer
- Safety glasses
- Work gloves
Building your own shed is a fantastic journey from planning to completion. This guide provides a framework for a simple, small shed. Remember, patience and careful planning are crucial. Enjoy the process, and soon you'll have a functional and attractive addition to your property!
DIY Pallet Shed: How to Create a Shed Using Free Plans and Pallets

DIY Pallet Shed: Constructing a Functional Outbuilding from Reclaimed Materials
The allure of a cost-effective and environmentally conscious construction project is undeniable. Building a shed from reclaimed pallets offers precisely that: a practical solution that minimizes expenditure and reduces waste. This comprehensive guide details the process of constructing a durable and aesthetically pleasing pallet shed, utilizing readily available free plans and readily sourced materials. While this project demands time and effort, the rewards of a custom-built shed crafted from recycled resources are substantial.
Phase 1: Planning and Preparation
Before embarking on the construction process, meticulous planning is paramount. This phase encompasses several crucial steps that will significantly impact the project's success.
A. Selecting Suitable Pallet Materials
Not all pallets are created equal. Identifying appropriate pallets is critical for structural integrity. Prioritize heat-treated pallets (marked with HT or ISPM 15) over chemically treated ones (marked with MB), as the latter may pose health risks. Inspect each pallet thoroughly for signs of rot, damage, or infestation. Choose pallets of consistent size and quality to simplify construction and ensure uniformity. The quantity required will depend on the desired dimensions of your shed.
B. Sourcing Free Plans
Numerous online resources offer free shed plans adaptable to pallet construction. Conduct thorough research to identify a plan aligning with your desired dimensions, aesthetic preferences, and skill level. Consider factors such as roof pitch, door placement, and window integration when making your selection. Download and print the chosen plans for easy reference throughout the construction process.
C. Acquiring Necessary Tools and Materials
A comprehensive tool inventory is essential for a successful construction. Essential tools include:
- Hammer
- Crowbar or pallet separator
- Circular saw or reciprocating saw
- Drill with various drill bits
- Screwdriver (both Phillips and flathead)
- Measuring tape
- Level
- Safety glasses
- Work gloves
- Safety boots
Beyond tools, you'll need additional materials like:
- Exterior-grade screws (various lengths)
- Metal brackets or connectors (for added strength)
- Roofing material (e.g., corrugated metal sheets, asphalt shingles)
- Optional: Paint or sealant for weather protection
- Optional: Plywood or other sheeting for interior walls or added weatherproofing
Phase 2: Construction Process
With plans and materials assembled, the construction phase commences. This section breaks down the process into manageable steps.
A. Foundation Preparation
While pallets are relatively lightweight, a stable foundation is crucial. A simple gravel base will suffice for smaller sheds, while larger structures may benefit from a more robust foundation like concrete slabs or treated lumber. Level the chosen area and compact the base material thoroughly before proceeding. Ensure the foundation is large enough to accommodate the footprint of the shed as outlined in your plans.
B. Frame Construction
Begin by assembling the shed's frame according to the chosen plans. This typically involves connecting pallets to create the walls and roof structure. Utilize screws and metal connectors to reinforce joints, enhancing structural integrity and durability. Regularly check measurements and ensure the frame remains square and level throughout the assembly process. Consider pre-assembling sections of the frame to simplify on-site construction.
C. Wall and Roof Installation
Once the frame is complete, install the remaining pallets to form the walls. Depending on the chosen plans, you might require additional materials to fill gaps or create a more aesthetically pleasing finish. Consider using plywood sheeting for added insulation and weather protection. The roof construction will depend on the chosen roofing material. Ensure proper overlapping of roofing materials to ensure adequate water runoff and weather protection.
D. Door and Window Installation
Incorporate doors and windows as outlined in the plans. You may need to cut pallet sections to create openings or use separate materials for doors and windows. Reinforce these openings with additional structural supports to ensure stability and durability. Use appropriate hinges and latches for doors and secure windows adequately to prevent accidental opening.
E. Finishing Touches
Once the shed's structure is complete, add finishing touches to enhance its appearance and durability. Apply a sealant or paint to protect the wood from moisture and weathering. This will significantly extend the life of your shed. You may also wish to add landscaping around the shed to enhance its overall aesthetic appeal. Consider additional features like shelves or workbenches based on intended shed use.
Phase 3: Post-Construction Considerations
After completing the shed, certain considerations remain crucial for its long-term functionality and preservation.
A. Regular Inspection
Regular inspection of the shed's structure is vital to identify and address any potential issues early on. Check for loose screws, damaged pallets, and signs of water damage. Promptly address any problems to prevent further deterioration. Seasonal inspections are highly recommended.
B. Maintenance and Repair
Preventative maintenance extends the lifespan of your pallet shed. Regularly clean and inspect the structure, and apply fresh sealant or paint as needed. Promptly address any necessary repairs to maintain structural integrity. Replacing damaged pallets is essential for maintaining the shed's functionality and preventing further damage.
C. Safety Precautions
Always prioritize safety during construction and ongoing maintenance. Use appropriate safety gear, including safety glasses and gloves, and ensure proper handling of tools and materials. Regularly assess safety hazards, especially when working at heights or with power tools.
By following these steps, you can successfully construct a functional and visually appealing pallet shed, demonstrating both resourcefulness and environmental consciousness. Remember that meticulous planning and careful execution are essential for a successful outcome. The resulting structure offers not only a practical storage solution but also a testament to the ingenuity of DIY construction.
Saturday, 16 November 2024
Ultimate Guide to Budget 12x20 Shed Plans with Loft

The Ultimate Guide to Budget-Friendly 12x20 Shed Plans with Loft
Hey there, fellow DIY enthusiasts! So you're dreaming of a spacious 12x20 shed, complete with a loft? Fantastic! But you're also on a budget, right? We get it. Building anything can get expensive, but with a bit of planning and some smart choices, you can absolutely achieve your shed goals without breaking the bank. This guide will walk you through everything you need to know to build your dream 12x20 shed with a loft, all while keeping your wallet happy.Planning Your Budget-Friendly 12x20 Shed with Loft
Before we even think about hammering a nail, let's get the planning stage nailed down. This is crucial, especially when you're working with a limited budget.Setting a Realistic Budget
First things first: how much can you realistically afford to spend? Be honest with yourself! It's tempting to underestimate, but overshooting your budget can lead to delays and stress. Consider all costs: materials, tools (renting vs. buying), permits, and even unexpected expenses (because, let's face it, they always happen!). A good rule of thumb is to add at least 10-15% to your initial estimate for those unforeseen hiccups.
Choosing Your Shed Style and Materials
A 12x20 shed offers tons of possibilities, but certain designs are more budget-friendly than others. Simple, gable-roofed sheds are generally less expensive to build than more complex designs. When choosing materials, consider pressure-treated lumber for the frame. It's durable and less prone to rot, a worthwhile investment in the long run, even if it costs a bit more upfront. For siding, you have options like vinyl (low maintenance, but can be more expensive) or metal (durable, relatively inexpensive). Don't be afraid to explore reclaimed or recycled materials if you can find them â" this can significantly reduce your costs!
Source Your Materials Wisely
This is where you can really save money! Don't just head to the nearest big-box store. Shop around! Compare prices from different lumber yards, home improvement stores, and even online retailers. Consider buying in bulk to get discounts. And remember, salvage yards and Craigslist can be treasure troves of affordable materials if you're willing to put in a little extra effort.
The Loft: Planning for Space and Support
The loft adds both functionality and charm, but it also requires careful planning. You'll need to incorporate strong support beams and consider the load-bearing capacity of the floor joists. This is not something to skimp on; a poorly constructed loft is a safety hazard. You'll likely need to buy extra lumber for the loft framing. Think about how youâll access the loft; a sturdy ladder or staircase is essential.
Essential Tools and Materials for Your Budget Shed
Let's talk about the essentials. Remember, renting tools can significantly reduce upfront costs. Consider your skillset and comfort level; renting specialized tools might be better than buying them if you're only building one shed. Here are some essential items:
- Measuring tape
- Level
- Hammer
- Circular saw (or hand saw if you're feeling ambitious!)
- Drill
- Screws and nails
- Pressure-treated lumber for the frame
- Siding material of your choice
- Roofing material (consider asphalt shingles for a budget-friendly option)
- Plywood for the floor and loft
- Insulation (optional, but recommended for a more comfortable space)
Step-by-Step Construction Guide (Simplified)
Building a shed is a multi-step process, but we can break it down into manageable chunks:
- Site Preparation: Level the ground, mark the dimensions, and ensure you have the proper permits.
- Foundation: Consider a simple concrete slab or gravel base. This is crucial for stability and longevity.
- Framing: This is where your pressure-treated lumber comes into play. Build the walls, ensuring they're square and plumb.
- Roof Construction: This step requires precision, so carefully follow your plans. A gable roof is generally easiest for DIYers.
- Siding and Roofing: Install your chosen siding and roofing materials. Take your time and ensure proper overlap.
- Loft Framing and Floor: Construct the loft framing, ensuring itâs securely attached to the main structure. Install the loft floor using plywood.
- Finishing Touches: Add doors, windows, and any other desired features.
Remember, this is a simplified overview. A detailed set of plans is essential for success! You can find many 12x20 shed plans online (some are free, others are paid), but be sure to check reviews before purchasing.
Tips for Staying on Budget
- Do as much of the work yourself as possible: This is the biggest cost-saver.
- Enlist help from friends or family: A helping hand (or two!) can speed up the process and make it more fun.
- Prioritize your purchases: Buy the essential materials first and add extras later as your budget allows.
- Don't be afraid to ask for advice: Experienced builders are usually happy to share their knowledge.
- Consider repurposing materials: Get creative and find ways to reuse materials wherever possible.
Commonly Asked Questions
Q: Do I need a building permit?
A: This depends on your local building codes. Check with your local authorities to determine whether you need a permit before you start building.
Q: How much will this actually cost?
A: The cost varies greatly depending on materials, location, and your choice of finishes. Expect to spend anywhere from $3,000 to $10,000 or more. Careful planning and resourcefulness are key to staying on the lower end of that spectrum.
Q: What's the best type of foundation for a 12x20 shed?
A: A concrete slab is ideal for stability and longevity, but a well-constructed gravel base is a more budget-friendly alternative.
Q: Can I build this shed myself if I'm a beginner?
A: Yes, but it will require patience, research, and potentially some help from more experienced builders. Start with simpler projects to build your skills before tackling a shed this size. Take your time and don't be afraid to ask for help!
Building your own 12x20 shed with a loft is a rewarding project! With careful planning, smart choices, and a bit of elbow grease, you can create a fantastic storage solution without emptying your bank account. Good luck and happy building!
Monday, 11 November 2024
DIY Guide to Building a Pole Barn for Cold Weather Areas
Pole barns, with their robust construction and adaptable design, are increasingly popular choices for a wide range of applications, from garages and workshops to agricultural structures and even residences. However, in cold weather climates, building a pole barn requires extra considerations to ensure optimal performance and longevity. This guide delves into the essential aspects of building a pole barn specifically tailored for frigid temperatures, offering detailed insights into materials, construction techniques, and crucial considerations for a successful project.
1. Foundation and Frost Lines:
Understanding Frost Depth: Unlike warmer climates, cold regions experience significant frost heave, where the ground expands as water freezes, potentially damaging structures. Determining the frost line depth in your area is paramount. Consult local building codes or a geotechnical engineer for accurate information.
Concrete Piers or Footings: While traditional concrete foundations are feasible, they can be costly. For pole barns, the most common approach is using concrete piers or footings that extend below the frost line. These provide a solid base while minimizing excavation and concrete use.
Pier Design and Placement: The size and spacing of piers depend on the pole barn's dimensions and intended use. Ensure proper load calculations to ensure adequate support. Consult an engineer for precise specifications.
Foundation Drainage: Effective drainage is crucial to prevent moisture accumulation around the piers, which can lead to frost heave. Install a gravel layer around the piers to facilitate drainage.
2. Pole Selection and Installation:
Choosing the Right Poles: For cold climates, select pressure-treated lumber or engineered wood products like glulam beams. These materials resist decay, insect infestations, and the harsh elements. Opt for poles with a minimum diameter of 6 inches for added strength.
Pole Placement and Spacing: The spacing between poles depends on the size and intended use of the barn. Ensure adequate support for the roof load and any other structural components. Consult a structural engineer for accurate specifications.
Setting the Poles: Carefully position the poles on the concrete piers or footings, using a level to ensure vertical alignment. Secure them with concrete or specialized anchoring systems.
3. Roofing System:
Insulated Roof Panels: Effective insulation is paramount in cold climates. Consider using insulated metal roof panels for their superior thermal resistance, durability, and low maintenance requirements.
Ventilation: Adequate ventilation is critical for preventing condensation buildup and maintaining optimal moisture levels within the barn. Install roof vents or ridge vents for proper air circulation.
Snow Load Considerations: Design the roof with a steep pitch to facilitate snow shedding and prevent excessive accumulation. Consult local building codes for snow load requirements in your area.
4. Wall Systems and Insulation:
Wall Construction: Pole barn walls are typically constructed with wood framing, insulated with fiberglass batts or foam boards, and clad with siding.
Insulation Considerations: Opt for insulation with high R-values for optimal thermal resistance. Consider using continuous insulation, such as rigid foam boards, for added protection.
Siding Materials: Choose durable siding materials that withstand harsh weather conditions. Metal siding is a popular choice for its longevity and low maintenance.
5. Heating and Climate Control:
Heating System Selection: A robust heating system is essential for a comfortable and functional pole barn in cold climates. Options include propane heaters, wood-burning stoves, or forced-air furnaces.
Energy Efficiency: Optimize energy efficiency with well-insulated walls and roof, efficient heating systems, and air sealing around doors and windows.
Moisture Control: Adequate ventilation is crucial for preventing condensation and moisture buildup, which can lead to mold growth and structural damage.
6. Additional Considerations:
Door Selection: Choose durable doors designed for cold weather conditions, with insulated panels and weather stripping.
Window Placement: Consider the placement and size of windows to maximize natural light while minimizing heat loss.
Electrical Wiring: Ensure adequate electrical wiring to accommodate your needs and meet local codes.
Safety: Implement safety measures like fire extinguishers and smoke detectors for a safe environment.
7. Building Codes and Permits:
Local Codes: Research and adhere to all local building codes and regulations, which may vary depending on your location.
Building Permits: Obtain the necessary building permits before starting construction.
8. Construction Techniques:
Professional Expertise: While building a pole barn is often a DIY project, consider hiring a professional for certain aspects like foundation work and roof construction, especially in challenging weather conditions.
Safety Precautions: Implement safety precautions throughout the construction process, including personal protective equipment and proper tool handling.
Conclusion:
Building a pole barn in a cold weather climate requires meticulous planning, high-quality materials, and adherence to specific construction techniques. By understanding the unique challenges and implementing the strategies outlined in this guide, you can build a durable, functional, and energy-efficient pole barn that will withstand the harshest winters. Remember, consulting with professionals like engineers and builders can ensure your project's success and long-term satisfaction.
How to Build a Pole Barn with a Focus on Strength and Durability
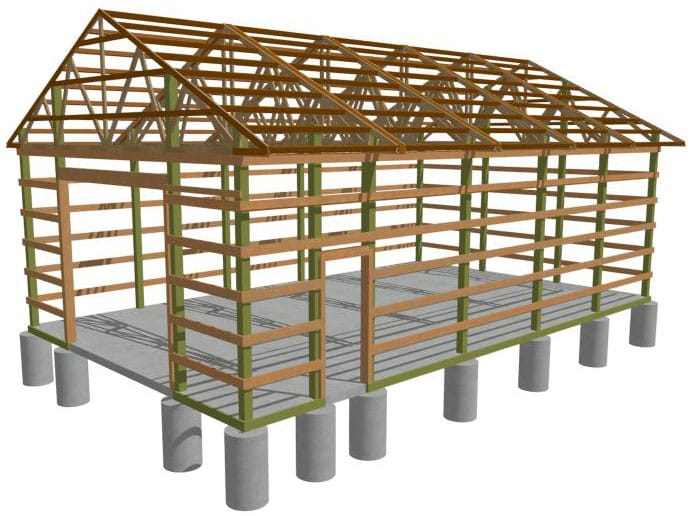
Pole barns, often referred to as post-frame buildings, have gained immense popularity due to their versatility, cost-effectiveness, and relative ease of construction. However, to ensure longevity and structural integrity, meticulous planning and construction techniques are paramount. This guide delves into the crucial aspects of building a pole barn with an emphasis on strength and durability.
1. Site Preparation and Foundation:
The foundation is the cornerstone of any structure, and pole barns are no exception. A well-prepared foundation will ensure the barn withstands the test of time and prevents future problems.
Site Selection: Choose a level or gently sloped site with good drainage to prevent water accumulation and soil erosion. Avoid areas prone to flooding or excessive moisture.
Soil Testing: Conduct a soil test to determine the bearing capacity of the soil. This will guide the choice of foundation type and the required depth of the posts.
Foundation Design:
Concrete Piers: This robust option involves setting concrete piers, typically 12-18 inches in diameter, into the ground. These piers provide excellent support and can be customized for varying load capacities.
Concrete Slabs: A continuous concrete slab offers a more robust foundation but requires a larger footprint and higher material costs.
Concrete Footings: Footings are smaller concrete blocks that support the base of the posts. They are suitable for lighter structures and shallower depths but require accurate placement.
Post Installation:
Post Depth: The depth of the posts should be determined based on soil bearing capacity, local frost line, and building code regulations. Aim for at least 4 feet below the frost line for optimal stability.
Concrete Encapsulation: Securely encase the bottom portion of the posts in concrete to prevent rot and ensure a solid connection to the foundation.
Post Spacing: The distance between posts will depend on the building's size, intended use, and load requirements. Generally, spacing should be no more than 8 feet apart.
Post Alignment: Use levels and plumb lines to ensure posts are perfectly vertical and aligned. This is crucial for structural stability and building aesthetics.
2. Framing and Walls:
The framing forms the skeleton of the pole barn, supporting the roof and providing the necessary strength for the walls.
Post Materials:
Lumber: Pressure-treated lumber is the most common choice for pole barn framing. Its resistance to rot and insects ensures long-lasting performance.
Steel Posts: Steel posts offer exceptional strength and durability, especially in areas prone to extreme weather conditions or heavy loads. They require proper installation and may necessitate specialized equipment.
Wall Framing:
Stud Spacing: Use standard 16-inch on-center spacing for wall studs, ensuring adequate support for sheathing and siding.
Wall Sheathing: OSB (Oriented Strand Board) or plywood are commonly used as wall sheathing, providing structural support and a smooth surface for siding.
Bracing: Proper bracing, such as diagonal sheathing or metal straps, is essential for resisting wind loads and enhancing structural stability.
3. Roofing System:
The roof of a pole barn faces the elements directly, so choosing the right system is vital.
Roof Framing:
Rafters: Use adequately sized rafters, typically 2x6 or 2x8 lumber, to support the roof sheathing and the weight of snow and wind loads.
Roof Truss System: For larger spans or complex roof shapes, pre-engineered roof trusses provide a cost-effective and structurally sound solution.
Roof Sheathing:
Solid Sheathing: Solid sheathing, such as plywood or OSB, is recommended for optimal strength and durability, especially in areas with high wind loads or heavy snow accumulation.
Open Sheathing: Open sheathing, like spaced 2x4 lumber, can be used for lighter roofs and may offer better ventilation. However, it requires careful consideration of the chosen roofing material.
Roofing Material:
Metal Roofing: Metal roofing offers exceptional durability, longevity, and low maintenance. It is also highly resistant to fire and wind damage.
Shingles: Asphalt shingles are a cost-effective option but require regular maintenance and may have a shorter lifespan compared to metal roofs.
Standing Seam Metal: This high-quality metal roofing option provides superior strength and aesthetic appeal, making it suitable for both residential and commercial applications.
4. Siding and Exterior Finishes:
The siding not only enhances the visual appeal of the barn but also protects the underlying structure from the elements.
Siding Materials:
Metal Siding: Metal siding offers exceptional durability, low maintenance, and a wide range of colors and styles.
Vinyl Siding: Vinyl siding is a budget-friendly option that comes in various colors and textures, offering a modern aesthetic.
Wood Siding: While offering a classic look, wood siding requires regular maintenance and may be susceptible to rot or insect damage.
Exterior Finishes:
Paint: Paint provides protection against UV rays, moisture, and weather damage, extending the lifespan of the siding. Choose high-quality paint specifically designed for exterior use.
Staining: Stain allows the natural beauty of the wood to shine through while providing protection against weathering.
5. Doors and Windows:
Doors and windows are essential for access, ventilation, and natural light.
Doors:
Overhead Doors: Overhead doors are ideal for large openings and provide easy access for vehicles or equipment.
Sliding Doors: Sliding doors offer space-saving solutions and are suitable for smaller openings.
Swinging Doors: Traditional swinging doors are cost-effective and readily available. Choose sturdy, weather-resistant materials for long-lasting performance.
Windows:
Placement: Consider the desired level of natural light and ventilation when positioning windows.
Glazing: Choose double-paned windows for better insulation and energy efficiency.
Window Frames: Select durable, weather-resistant materials such as aluminum, vinyl, or fiberglass for the window frames.
6. Interior Finishing and Insulation:
The interior finish and insulation contribute to the comfort and functionality of the barn.
Interior Walls:
Drywall: Drywall provides a smooth and paintable surface for interior walls.
Plywood: Plywood offers a durable and cost-effective option, often used for unfinished interior spaces.
Paneling: Paneling adds a rustic aesthetic and can be a suitable choice for barns used for storage or workshops.
Insulation:
Blown-in Cellulose: Cellulose insulation is a cost-effective and environmentally friendly option.
Fiberglass Batts: Fiberglass batts are a common choice and offer good insulation values.
Spray Foam Insulation: Spray foam provides superior insulation and air sealing properties but can be more expensive.
7. Electrical and Plumbing:
Electrical and plumbing installations require careful planning and adherence to local building codes.
Electrical Wiring:
Wiring Materials: Use appropriately rated wiring and protective devices to ensure safe and reliable electrical service.
Electrical Outlets: Provide adequate electrical outlets for lighting, tools, and other equipment.
Ground Fault Circuit Interrupters (GFCIs): Install GFCIs in areas with moisture or potential for water contact, such as bathrooms and kitchens.
Plumbing:
Water Supply: Install a reliable water supply system, including pipes, valves, and a water heater if necessary.
Drainage: Provide adequate drainage for waste water, ensuring proper connection to a septic system or municipal sewer lines.
8. Building Codes and Permits:
It is crucial to consult local building codes and obtain the necessary permits for your pole barn project.
Building Codes: Building codes vary by location and may specify requirements for foundation depth, framing, roofing, and other aspects of construction.
Permits: Obtain the necessary permits before beginning construction, including foundation permits, building permits, and electrical permits.
9. Professional Assistance:
Consider consulting with a qualified professional for complex pole barn projects or if you lack construction experience.
Structural Engineers: Structural engineers can provide professional advice on design, foundation calculations, and load-bearing requirements.
Contractors: Experienced pole barn contractors can handle the entire construction process, from foundation to finishing.
Conclusion:
Building a durable and long-lasting pole barn requires meticulous planning and attention to detail. By following these guidelines and implementing proper construction techniques, you can ensure your pole barn provides years of reliable service and stands the test of time.
DIY Pole Barn: How to Add a Loft for Extra Storage

Hey there, fellow DIYer! So you've got a trusty pole barn, a haven for your tools, projects, and maybe even a car or two. But let's be real, space is always at a premium. What if I told you there's a way to double (or even triple!) your storage space without breaking the bank? That's right, we're talking about adding a loft to your pole barn!
Now, before you envision yourself building a complex, multi-level structure, let me assure you, this project is totally achievable for a DIY enthusiast. Think of it as an elevated platform, a hidden treasure trove above your current setup. It's a project that can be tackled in phases, allowing you to enjoy the fruits of your labor even as you progress.
So, let's dive into the exciting world of pole barn lofts!
### Planning is Key: Laying the Foundation for Success
The first step, as with any construction project, is meticulous planning. You need to answer some crucial questions:
1. What's the Purpose? Are you aiming for a dedicated storage space, a workshop, or something more ambitious like a guest room? This will determine the loft's size, flooring needs, and even its design.
2. What are Your Limitations? Consider the existing structure's strength, your budget, and any local building codes. You don't want to overload your barn or face unforeseen penalties later on.
3. How High Can You Go? The height of your barn's sidewalls will determine the height of your loft, so choose a height that's comfortable for you to access and utilize.
4. What's the Access? Think about how you'll get your belongings up there. Will you need a ladder, a stairway, or even a small lift? This will impact the design and placement of the access point.
5. What about the Floor? Plywood is a cost-effective option, but consider adding a layer of subfloor for extra strength and noise reduction. Think about what you'll be storing and whether you need a specialized floor, like one suitable for vehicles or heavy machinery.
6. Don't Forget the Finishing Touches! Will you want to insulate your loft for climate control? How will you handle lighting and ventilation? These are considerations to make as you finalize your plan.
### Building Your Loft: A Step-by-Step Guide
Now that you've got your plan in place, it's time to roll up your sleeves and get building! This process can be broken down into manageable stages:
1. The Framing Foundation: This is where you'll build the skeletal structure of your loft. Use treated lumber for framing, ensuring they are properly anchored to the barn's existing structure. This involves bolting the framing directly to the beams or using metal brackets for extra support.
2. Flooring: The Solid Base: Once your frame is in place, it's time to lay the flooring. Begin with plywood, securing each sheet to the joists using screws. If you're adding a subfloor, lay it down first, ensuring it's level and securely attached.
3. Access Point: Your Gateway to the Loft: Now, it's time to create the way you'll access your loft. This can be as simple as a sturdy ladder or as intricate as a winding staircase. Consider the space needed for your chosen access method and its placement within the barn.
4. Finishing Touches: Making it Your Own: You've built your loft! Now comes the fun part: adding the finishing touches. This could involve installing insulation, building out walls, or even adding a small window for natural light. Choose the elements that make your loft functional and enjoyable.
### Safety First: Don't Take Shortcuts
Building a loft is a rewarding project, but it's crucial to prioritize safety. Here are some essential reminders:
Always wear safety gear: This includes safety glasses, work gloves, and sturdy footwear.
Follow building codes: Ensure your project meets all local regulations.
Use proper lifting techniques: Don't lift heavy materials alone; enlist help.
Don't overestimate your capabilities: Ask for help from a qualified professional if you're unsure about any aspect of the project.
Check for stability: Before you start using your loft, make sure the structure is solid and safe.
### More Than Just Storage: Unleashing the Possibilities
A loft isn't just about extra storage; it opens up a world of possibilities for your pole barn:
Workshop Oasis: Turn your loft into a dedicated workspace for hobbies, crafts, or even light industrial work.
Guest Room Retreat: Transform the loft into a cozy and private guest room, complete with a bed, seating, and even a mini-kitchenette.
Playroom Paradise: Create a fun-filled haven for kids, complete with a play area, storage for toys, and a dedicated space for crafts and creativity.
Home Office Haven: Enjoy a quiet and productive workspace with a dedicated office setup in your loft.
### Embrace the Journey, Celebrate the Outcome!
Adding a loft to your pole barn is a rewarding project, one that allows you to maximize your space and unlock new possibilities. Remember, it's a journey, and every step, from planning to finishing touches, brings you closer to a more efficient and enjoyable pole barn.
So, gather your tools, unleash your creativity, and get ready to turn your pole barn into a storage and functionality powerhouse! Happy building!
How to Build a Pole Barn with a High Ceiling for Equipment
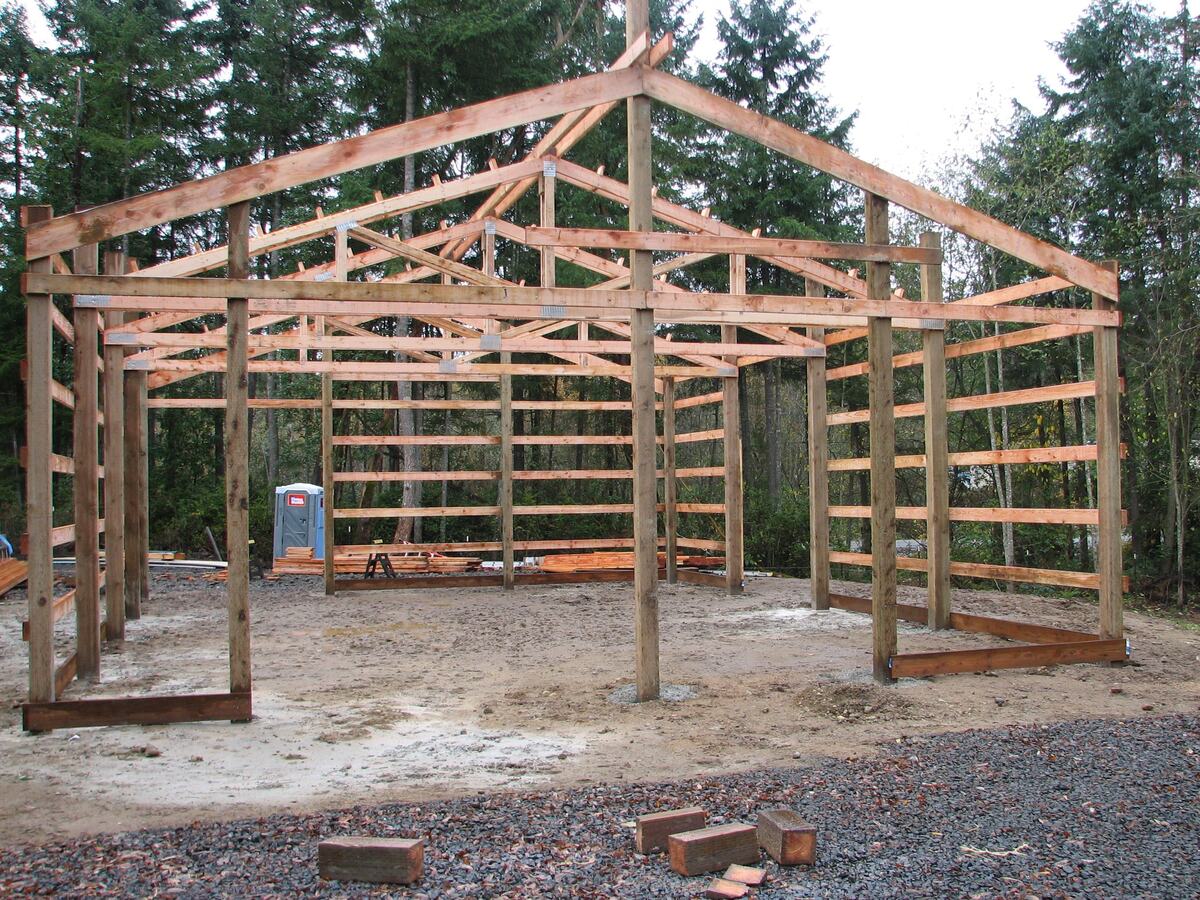
Okay, so you're tired of your equipment crammed into a tiny garage or left exposed to the elements. You want a dedicated space, a haven for your prized possessions, and a workspace that doesn't make you feel like you're in a sardine can. Enter the pole barn: a sturdy, versatile structure that offers a surprisingly spacious and functional solution. And with a high ceiling, you can literally take your aspirations to new heights!
Why Pole Barns?
Let's be real, pole barns aren't just for storing hay bales and tractors anymore. They're becoming increasingly popular for everything from workshops and garages to home offices and even living spaces. Why? Because they offer a whole lot of bang for your buck.
Cost-Effective: You're looking at a significantly lower price tag compared to traditional construction. Pole barns use less material, and the DIY aspect can save you a pretty penny (more on that later).
Quick Construction: The simplicity of the design means you can get your pole barn up and running in a fraction of the time it takes to build a conventional structure.
Versatile: Pole barns are incredibly adaptable. You can customize the size, layout, and even add features like windows, doors, and even a loft for extra storage or living space.
Durable: Constructed with sturdy posts and a strong steel roof, pole barns are built to withstand even the harshest weather conditions.
Going High: The Importance of Ceiling Height
Now, let's talk about that high ceiling. It's not just about making your barn feel grand (although it definitely does that!), it's all about functionality.
Equipment Storage: High ceilings mean you can store even the tallest equipment without having to worry about hitting your head or needing a forklift. Imagine the possibilities! Boats, ATVs, RVs, or maybe even a classic car â" all tucked away safely and conveniently.
Open Workspace: A high ceiling gives you a sense of openness and spaciousness, making your workshop feel larger and less cluttered. This is especially important if you work with large machinery or projects that require plenty of room to move around.
Ventilation and Lighting: Higher ceilings allow for better air circulation, preventing moisture build-up and creating a more comfortable working environment. Plus, you have more room for overhead lighting, illuminating your workspace effectively.
Planning Your High-Ceiling Pole Barn
Now, before you start digging holes and mixing concrete, there are a few things you need to consider:
1. Local Building Codes: Every area has its own set of regulations regarding building permits, setbacks, and construction standards. Check with your local building department to ensure your pole barn meets all the requirements.
2. Design and Layout: Think about how you want to use your pole barn. Do you need a dedicated workshop area? Do you need separate sections for storage and workspaces? Consider things like doors, windows, electrical outlets, and any other features you want to include.
3. Material Choice: Pole barns are typically built with pressure-treated wood posts, steel roofing, and plywood siding. However, there are other options available depending on your budget and aesthetic preferences.
4. Foundation: For high ceilings, a concrete foundation is often the most durable and stable option. It provides a solid base for your structure and helps prevent settling over time.
The DIY vs. Hiring Out Dilemma
Building a pole barn is a project that can be tackled by DIY enthusiasts, but it's not for the faint of heart. You need to be comfortable with carpentry, basic construction skills, and heavy lifting.
DIY Pros: You save money on labor costs and have complete control over the project. Plus, there's a sense of accomplishment that comes with building something yourself.
DIY Cons: You'll need to invest in tools and equipment, and the project may take longer than hiring a professional. You also need to be prepared for potential setbacks and challenges.
Hiring a Contractor:
If you're not confident in your DIY skills, hiring a professional builder can be a good option.
Contractor Pros: You'll have a team of experienced professionals who can ensure the project is completed to code and on time. They can also handle the more challenging aspects of construction, like foundation work and roof installation.
Contractor Cons: Hiring a contractor will cost you more, and you may have less control over the design and materials used.
The Build Process: A Glimpse into the Action
Whether you go the DIY route or hire a contractor, the basic steps for building a pole barn with a high ceiling are similar:
1. Site Preparation: Clear the site, mark the foundation lines, and excavate the holes for the posts.
2. Foundation Construction: Pour the concrete foundation, making sure it's level and strong enough to support the weight of the structure.
3. Post Installation: Set the pressure-treated posts into the concrete foundation.
4. Framing: Build the roof trusses and install them on top of the posts.
5. Roofing: Install the steel roofing panels, ensuring proper ventilation and drainage.
6. Siding: Add the plywood siding, choosing the material and finish that suits your style.
7. Interior Finishing: Install insulation, drywall, and any interior finishes you desire.
High Ceilings: Extra Considerations
Building a high-ceiling pole barn requires a few extra considerations to ensure safety and stability:
Stronger Posts: Use larger diameter pressure-treated posts to support the increased weight of the roof.
Robust Roof Trusses: Choose trusses designed to handle the span and weight of a higher roof.
Proper Bracing: Ensure the roof trusses and posts are adequately braced to prevent sagging and maintain stability.
Access: Consider how you will access the higher areas of your pole barn for maintenance and repairs. A ladder or platform lift might be necessary.
Let Your Imagination Run Wild
With a high-ceiling pole barn, the possibilities are endless. From a fully-equipped workshop to a spacious showroom, to a cozy getaway with a loft overlooking your property, the choice is yours.
Remember, building a pole barn is a significant investment, but it's an investment in your future. With careful planning, you can create a versatile, durable, and beautiful space that will serve you well for years to come.
Sunday, 10 November 2024
Diy pole shed plans that wonât drain your wallet
Hey there, fellow DIYer! Tired of cramming your tools and projects into a cluttered garage? Dreaming of a spacious workshop or a place to park your prized possessions? Well, you're not alone. Building a pole barn is a popular choice for folks who want a functional, affordable space.
But let's be real, construction can be expensive. So, how do you build a pole barn without breaking the bank? It's all about smart planning and some DIY savvy. Let's dive into how to create a budget-friendly pole shed that won't leave you feeling drained:
First Things First: Planning is King
Before you start grabbing tools, it's crucial to have a solid plan. Here's how to get started:
Determine the Purpose: What will you use the pole barn for? Storage, workshop, vehicle shelter, or all of the above? Knowing your purpose will help you decide on size, features, and materials.
Location, Location, Location: Choose a level spot on your property that has good drainage. Consider access to utilities and the impact on your landscaping.
Size and Shape: Measure out your needs and sketch a simple plan. Remember, you can always add on later. Keep it simple and functional!
Building Codes and Permits: Check with your local building department for any necessary permits and building codes. It might seem like a hassle, but it's essential for safety and compliance.
Materials: Choosing Wisely
Now, the fun part - picking materials! The key to keeping costs down is to be smart with your choices. Here's what I recommend:
Pole Barn Posts: Treated lumber is essential to prevent rot. Consider pressure-treated pine or cedar, which can be more expensive but will last longer. You can also find good deals on used poles from demolition projects.
Roofing: Metal roofing is affordable, durable, and easy to install. Consider corrugated metal sheets for a classic pole barn look.
Siding: Again, metal siding is a budget-friendly option. It's low-maintenance and comes in a variety of colors.
Framing Lumber: Standard dimensional lumber like 2x4s and 2x6s will do the job. Look for sales at your local lumberyard, and don't hesitate to ask for discounts for bulk orders.
Windows and Doors: Consider simple, functional windows and doors. You can save money by installing them yourself.
DIY and Saving Money
The beauty of building a pole barn is that it's a great project for DIYers of all skill levels. Here are some ways to maximize your savings:
Do the Work Yourself: By tackling as much of the construction as possible, you'll save on labor costs. Plus, it's a rewarding experience!
Don't Be Afraid to Ask for Help: Need a hand with the heavier lifting? Enlist friends or family to help out. They'll appreciate the free beer, and you'll get the job done quicker.
Shop Around: Compare prices at different lumberyards and home improvement stores. You might be surprised at the differences.
Consider Reclaimed Materials: Don't overlook the potential of reclaimed wood, windows, or doors. You can find amazing deals on salvaged materials.
Building Basics: The Essential Steps
Now, let's talk about the actual construction. It's not rocket science, but it does require some planning and careful execution. Here's a general overview of the steps:
1. Site Preparation: Clear the area and level the ground. This is crucial for a stable structure.
2. Set the Posts: Dig holes for your posts, ensuring they're the right depth and spacing. Use concrete to secure the posts.
3. Erect the Frame: Attach the horizontal beams to the posts to create the framework. Use bolts and heavy-duty brackets for secure connections.
4. Install Roofing: Lay the roofing over the frame. Be sure to use proper flashing to prevent leaks.
5. Add Siding: Install siding to protect the building and give it a finished look.
6. Finishing Touches: Install windows, doors, and any other features you desire.
Tips and Tricks:
Don't rush the process: Take your time and do things right. It's better to be thorough than to cut corners.
Use quality tools: Invest in a few good tools, such as a power drill, level, and saw. They'll make your job easier and save you time.
Be Safe: Always follow safety precautions, wear appropriate gear, and use common sense.
Get Creative: Add your own personal touches to make your pole barn truly unique.
Enjoy Your New Space!
Building a pole barn can be a rewarding experience. It's a chance to create a functional space that suits your needs and reflects your own style. So, roll up your sleeves, grab your tools, and get started! You'll be amazed at what you can accomplish with a little planning and a lot of DIY spirit.
Remember, building a budget-friendly pole barn is all about smart choices and hard work. With a little creativity and a lot of dedication, you can have the space you've always dreamed of without breaking the bank.
Step-by-step guide for building a sturdy 12x16 shed

Hey there, DIY enthusiasts! Are you ready to tackle a project that will add value to your property AND give you a sense of accomplishment? Building a 12x16 shed is a fantastic undertaking, and I'm here to guide you through the process step-by-step, making it a breeze.
Don't worry, you don't need to be a seasoned carpenter to tackle this project. With a little planning, the right tools, and a sprinkle of patience, you'll be able to create a sturdy and functional shed that will be the envy of the neighborhood (or at least your block!).
### 1. Planning: Laying the Foundation
Before you dive into the construction, we need to make a plan. This is like the blueprint for your shed, ensuring everything fits together perfectly.
a. Know Your Local Codes:
First things first, check with your local building department about any regulations or permits required for building a shed. They might have rules regarding size, setbacks, and even the type of foundation you can use. It's always better to be safe than sorry, right?
b. Choosing a Location:
Pick a spot for your shed that's level and accessible, with good drainage. You'll want to consider sun exposure, proximity to your house, and ease of access for your future shed.
c. Decide on the Foundation:
Now, the fun part - the foundation. Do you want a concrete slab, a block foundation, or maybe a simple pier foundation?
Concrete slab: This is the most robust option and requires a concrete pour, but it's also more expensive.
Block foundation: Blocks are easier to lay and can be more budget-friendly, but they might require more excavation.
Pier foundation: This is the easiest and least expensive option, especially if you're on a budget. It involves digging holes and setting concrete piers, which are then topped with a wood frame.
Think about what makes sense for your needs and your budget.
d. Design and Materials:
Sketch out your shed! What features do you want? Doors, windows, shelves, a loft? Decide on the type of siding, roofing, and any finishing touches you'd like to add.
This is also the time to choose your materials. Choose pressure-treated lumber for the foundation and framing for longer life and resistance to moisture.
### 2. Getting Down to Business: Building the Foundation
Now that you have your plan, it's time to break out the tools and get dirty!
a. Prep the Site:
Clear any vegetation, level the ground, and mark out the dimensions of your shed.
b. Pouring Concrete (if you chose that option):
Dig out the area for the concrete slab.
Set up forms, making sure they're level and secure.
Mix the concrete according to the manufacturer's instructions.
Pour the concrete into the forms, and vibrate it to eliminate air pockets.
Allow the concrete to cure for at least 24 hours before you start building.
c. Laying Blocks (if you chose that option):
Excavate the area for the blocks.
Set up a level bed of mortar.
Lay the blocks in a row, using a level to ensure everything is straight.
Fill the spaces between the blocks with mortar.
Allow the mortar to cure for at least 24 hours.
d. Building Pier Foundation:
Dig holes for the piers, spaced according to your plan.
Fill the holes with concrete, ensuring the piers are level and stable.
Allow the concrete to cure for at least 24 hours.
Build a wood frame on top of the piers using pressure-treated lumber.
### 3. Framing: The Bones of Your Shed
Now that the foundation is set, it's time to give your shed some bones.
a. Framing the Walls:
Cut the wall studs to the correct height.
Attach the studs to the bottom plates using a nail gun or screws.
Add top plates to the studs.
Use diagonal bracing for added stability.
b. Framing the Roof:
Cut the roof rafters to the correct length.
Attach the rafters to the top plates using a nail gun or screws.
Install the roof sheathing (plywood) to provide a solid base for the roofing.
Add a ridge board to the top of the rafters, providing support for the roof.
### 4. Sheathing and Siding: Protecting Your Shed
Now it's time to give your shed a skin and some protection.
a. Sheathing:
Attach sheathing (plywood or OSB) to the walls and roof framing for additional strength and insulation.
b. Siding:
Choose your desired siding - wood, vinyl, metal, or fiber cement.
Cut the siding pieces and attach them to the sheathing, using nails or screws.
### 5. Roofing: Keeping the Elements Out
It's getting close! Now let's put a roof over your shed.
a. Install the Roof Underlayment:
Install a waterproof underlayment over the sheathing to create a barrier against leaks.
b. Install the Roofing Material:
Choose your roofing material, like shingles, metal, or tile.
Follow the manufacturer's instructions for installation.
### 6. Adding Doors and Windows: Letting the Light In (and Out)
Time to make your shed functional!
a. Install the Doors:
Choose your doors, considering size and style.
Cut the door frame and install it using screws or nails.
Hang the door using hinges.
Add a lockset.
b. Install the Windows:
Choose your windows - casement, double-hung, or sliding.
Cut the window frame and install it using screws or nails.
Install the window glass or panes.
### 7. Finishing Touches: Making it Your Own
It's almost time to move your stuff into your new shed!
a. Adding Insulation:
Install insulation in the walls and ceiling for better temperature control.
b. Installing a Floor:
If you want a finished floor, add a layer of plywood or subfloor to the foundation.
Then, lay down your preferred flooring - tiles, laminate, or even carpeting.
c. Paint or Stain:
Add a coat of paint or stain to the exterior and interior of your shed for a finished look.
### 8. Celebrate Your Accomplishment!
Now that your shed is complete, celebrate your hard work! You've just built a sturdy and functional addition to your property, and you can take pride in your accomplishment. Enjoy your new shed!
### Tips for Success:
Plan carefully: A well-thought-out plan will save you time and headaches in the long run.
Use the right tools: Don't be afraid to invest in the right tools - they'll make the job easier and faster.
Ask for help: Don't be afraid to ask for help from a friend or family member, especially for the heavier tasks.
Take your time: Building a shed is a process. Don't rush it, and enjoy the experience.
Building a shed might seem daunting, but with this step-by-step guide, you'll be surprised at how manageable it is. Remember, it's all about taking it one step at a time and enjoying the journey. Good luck, and happy building!
12x20 storage shed: the ultimate diy project
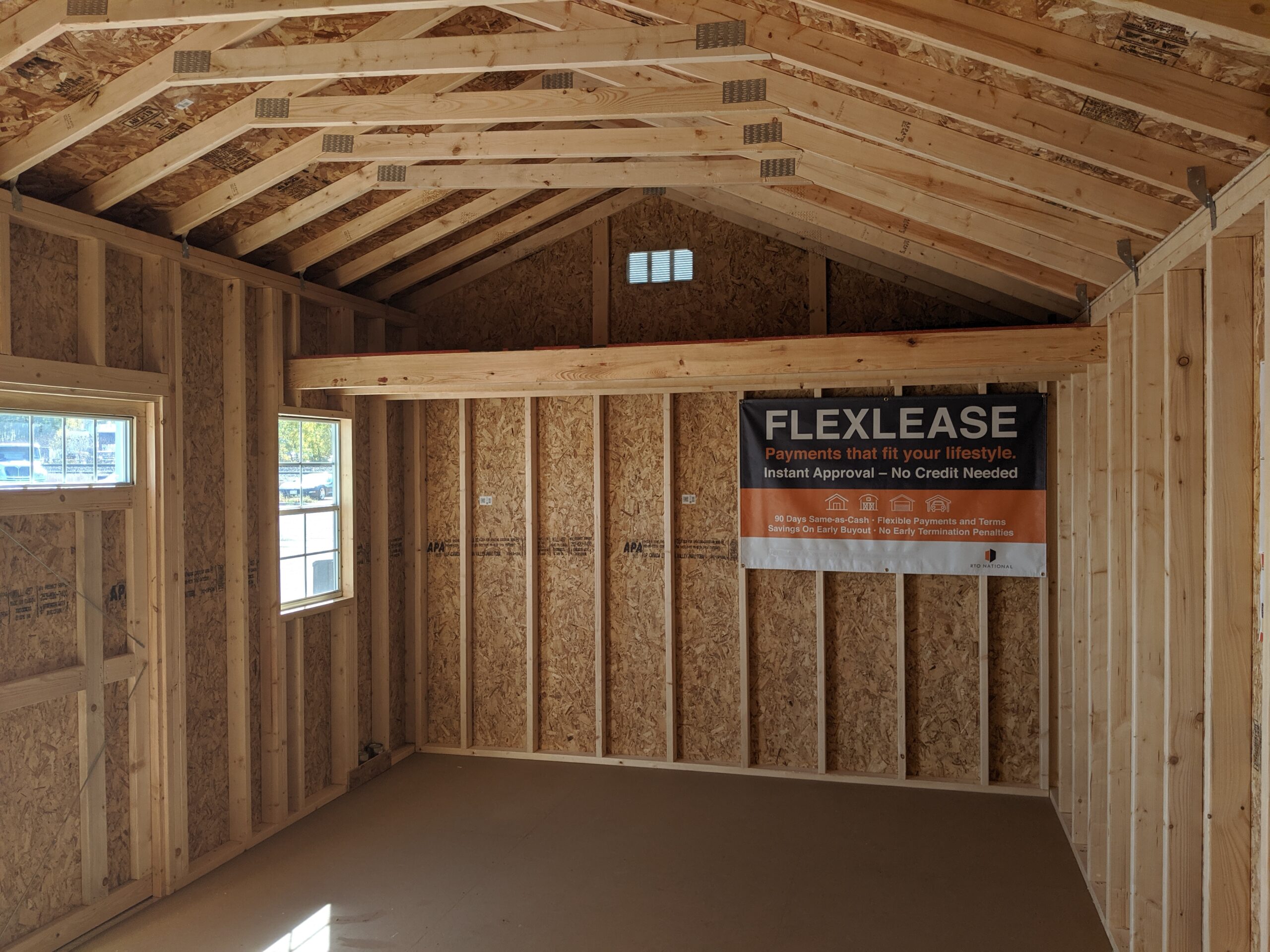
Okay, so you've got stuff. A lot of stuff. The garage is overflowing, the attic is a graveyard of forgotten dreams, and the basement is starting to resemble a hobbit hole. Sound familiar?
Well, fret no more, my friend! You're not alone in this battle against clutter. And guess what? You don't need to call in the professionals to solve your storage woes. We're going to build a 12x20 storage shed - a sturdy, weather-resistant sanctuary for all your beloved belongings.
Get ready for a DIY adventure that'll leave you feeling like a master craftsman (even if you've never picked up a hammer before!).
Step 1: Planning is Key - Like, Seriously!
Before you even think about grabbing a toolbox, we need a plan. A solid plan. Think of it as the blueprints for your storage masterpiece.
Location, Location, Location: Where will your shed reside? Make sure it's on level ground, accessible, and doesn't violate any pesky HOA rules (don't want to end up with a backyard brawl!).
Budget Breakdown: How much are you willing to spend? Factor in materials, tools, permits, and any potential surprises. It's always good to have a little wiggle room in your budget.
Design Decisions: What type of roof? Single-slope, gable, or something more fancy? Do you want windows? A door? Maybe a mini-porch for hanging out? This is your chance to let your creativity shine (within reason, of course!).
Step 2: Gather Your Tools & Materials
Time to get your hands dirty! But first, let's assemble the troops (aka your tools and materials).
Tools:
Measuring Tape: Your trusty sidekick for precise measurements.
Level: Keeps things straight and even.
Hammer: For driving those nails (or screws) with gusto.
Saw: For cutting those lumber giants down to size.
Drill: Makes those screws go in like butter.
Safety Glasses: Protect those precious peepers.
Work Gloves: Keep your hands safe and your grip strong.
Other Handy Helpers: You might also need a circular saw, a tape measure, a utility knife, and some basic hand tools.
Materials:
Lumber: The backbone of your shed. Choose pressure-treated lumber for the foundation and floor joists to withstand moisture.
Plywood: For sheathing and subfloor.
Roofing Shingles: For a weather-tight and stylish roof.
Windows and Doors: Let in some light and provide easy access.
Hardware: Nails, screws, hinges, handles, and more.
Insulation: Optional, but can help with temperature control.
Paint or Stain: Give your shed a personal touch and protect it from the elements.
Step 3: Foundation - The Bedrock of Your Shed
Now we're getting down to business!
Laying the Foundation: This is the most crucial part. A solid foundation is essential for a stable and long-lasting shed. You can opt for a concrete slab, a gravel base, or even a wooden platform.
Level It Out: Use a level to make sure your foundation is perfectly flat.
Anchor It Down: Secure your foundation to the ground using concrete anchors or rebar.
Step 4: Framing - The Skeleton of Your Shed
Time to build the bones of your storage masterpiece!
Wall Framing: Cut and assemble your wall studs according to your design. Remember to install header beams for window and door openings.
Floor Joists: Connect the floor joists to the foundation and ensure they are spaced evenly.
Roof Framing: Build your roof trusses or rafters according to your chosen roof type.
Step 5: Sheathing and Siding - Dressing It Up
Okay, our shed is starting to take shape! Let's add some muscle and style.
Sheathing: Attach plywood sheathing to the walls and roof to create a solid base for siding and roofing.
Siding: Choose your preferred siding material - wood, vinyl, or composite - and install it according to the manufacturer's instructions.
Step 6: Roofing - Protecting Your Haven
Time to keep those pesky rain clouds at bay!
Underlayment: Install a layer of roofing underlayment over the sheathing to provide an extra layer of protection.
Shingles: Secure your chosen roofing shingles to the roof, following the manufacturer's guidelines.
Step 7: Windows and Doors - Letting Light and Access In
Let's add some light and accessibility to your shed!
Window Installation: Carefully cut openings for your windows and install them according to the manufacturer's instructions.
Door Installation: Install your door in the designated opening, making sure the hinges are aligned and the door swings smoothly.
Step 8: Finishing Touches - Adding Your Personal Style
Your shed is almost ready for its grand opening! Time to add those finishing touches.
Insulation: If desired, install insulation in the walls and ceiling for temperature regulation.
Painting or Staining: Give your shed a fresh coat of paint or stain to protect it and add your personal style.
Finishing Touches: Add trim, gutters, and any other decorative elements you desire.
Step 9: The Grand Opening - Celebrate Your Accomplishment!
And there you have it! Your very own 12x20 storage shed. Celebrate your accomplishment with a well-deserved break, a cold beverage, and a big smile!
A Few Words of Wisdom:
Safety First: Always wear safety gear and follow proper safety procedures.
Don't Rush It: Take your time and don't be afraid to ask for help.
Embrace the Unexpected: Building a shed is a journey, and there will be challenges along the way.
Enjoy the Process: Take pride in your work and have fun with the project!
So, are you ready to embark on your DIY adventure? With a little planning, effort, and perhaps a few helpful hands, you can create a storage solution that is both practical and satisfying. Go on, unleash your inner craftsman and conquer the clutter! You've got this!
Diy 8x12 shed: a simple plan for your dream shed

Hey there, fellow DIY enthusiast! Ever dreamt of a cozy little shed in your backyard, a haven for your tools, a workshop for your projects, or maybe just a peaceful place to relax with a good book and a cup of coffee? Building your own 8x12 shed is more achievable than you think, even if you've never tackled a project this big before.
This guide will walk you through the process, step by step, with a focus on simplicity and clarity. Let's build that dream shed together!
1. Planning & Preparation
First things first, let's get organized! Planning is crucial for a smooth build.
a) Choosing Your Shed Location: Think about the sun, drainage, and accessibility. You'll want your shed to be well-lit and easy to get to.
b) Design & Dimensions: Sketch out your shed on paper or use a simple online shed design tool. Consider how you'll use it to decide on features like windows, doors, and shelves.
c) Building Materials: Determine the materials you'll need:
Foundation: Concrete piers, concrete slab, or a treated lumber base are common options.
Framing: 2x4 or 2x6 lumber for the walls and roof.
Sheathing: Plywood or OSB for walls and roof.
Roofing: Asphalt shingles, metal roofing, or even cedar shakes are all great choices.
Siding: Vinyl siding, wood siding, or even corrugated metal are popular options.
d) Tools and Equipment:
Measuring tape, level, saw, hammer, drill, drill bits, nails, screws, safety glasses, gloves, and a good pair of work boots are essential.
e) Permit Requirements: Check with your local building department about any permits needed before you begin construction.
2. Foundation: Laying the Groundwork
The foundation is crucial to your shed's stability.
a) Concrete Piers: This option is straightforward and cost-effective. Dig holes, set concrete piers, and let them cure.
b) Concrete Slab: If you want a solid base, pouring a concrete slab is an option.
c) Treated Lumber Base: A simple but durable option. Use treated lumber to build a platform that sits on compacted gravel.
3. Framing: Building the Bones
Now comes the fun part â" building the frame!
a) Walls: Cut and assemble wall frames, ensuring they are plumb and square.
b) Floor Joists: Lay down floor joists on the foundation, connecting them with joist hangers.
c) Roof Trusses: Choose prefabricated trusses or build your own using rafter plans. Attach them to the wall frames, ensuring they are properly supported.
d) Sheathing: Cover the walls and roof with plywood or OSB.
4. Roofing: Protecting Your Investment
a) Underlayment: Install felt paper or a synthetic underlayment over the sheathing to protect your roof from moisture.
b) Shingles: Choose your desired roofing material and follow manufacturer instructions for installation.
c) Flashing: Install flashing around vents, chimneys, and roof edges to prevent leaks.
5. Siding and Trim: The Finishing Touches
a) Siding: Choose your desired siding material and install it according to manufacturer instructions.
b) Trim: Add window and door trim, along with any other desired trim details.
6. Windows and Doors: Bringing in the Light
a) Window Installation: Install your windows, ensuring they are properly sealed and weatherproofed.
b) Door Installation: Install your door, ensuring it is level and properly secured.
7. Interior Work: Personalizing Your Space
a) Flooring: Install flooring - concrete, wood, or vinyl are popular choices.
b) Insulation: Add insulation to the walls and ceiling for added comfort.
c) Interior Finishing: Paint or finish the walls and ceiling to your liking.
d) Electrical Work: If you're planning on adding electricity, hire a qualified electrician for this step.
8. Enjoying Your New Shed!
Congratulations! You've built your own 8x12 dream shed. Now it's time to enjoy your new space! Take some time to organize and personalize it to fit your needs.
Helpful Tips:
Don't be afraid to ask for help: Even experienced builders call on friends and family for assistance.
Take your time: Building a shed is a rewarding process. Don't rush it!
Safety First: Always wear safety glasses and gloves when working with power tools.
Building your own 8x12 shed can be a fun and fulfilling project. With careful planning and a little bit of elbow grease, you can create a space that you'll love for years to come.
Remember, this is just a general guide. Be sure to consult with professionals for specific instructions and advice on your local building codes and regulations.
Happy building!